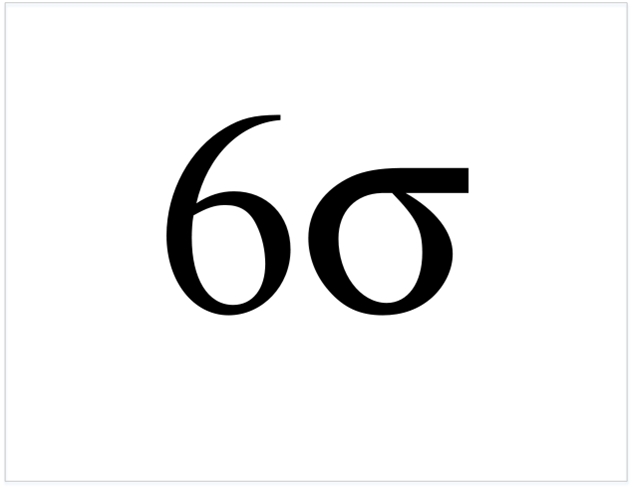
Variation occurs everywhere! Understanding and reducing variation in service, manufacturing and sales and marketing processes are key to achieving Six Sigma performance. Measurement and statistical analysis are key elements for a successful program. The Six Sigma process and its linkage to Lean Production System will be discussed. The course is highly interactive where delegates will run a business simulation process applying their new knowledge to approach six sigma performances.
By the end of this course delegates will be able to:
Team Leaders, Managers, Superintendents, General Supervisors, Officers, Supervisors, Line Managers, HR Professionals
CDGA attendance certificate will be issued to all attendees completing minimum of 75% of the total course duration.
Code | Date | Venue | Fees | Register |
---|---|---|---|---|
QUA125-03 | 29-09-2025 | Istanbul | USD 5950 | |
QUA125-04 | 14-12-2025 | Dubai | USD 5450 |
Engineering and Production Professionals all over the world are passionate about Six Sigma. Six Sigma is a methodology to develop great products and services that your customers love. Six Sigma is ...
Six Sigma is the comprehensive business improvement strategy made famous by organizations such as Motorola, General Electric, Honeywell and others, which has been used to generate significant improvem ...
The Six Sigma methodology is a systematic application focused on achieving significant financial results and increasing customer satisfaction. When properly deployed on carefully selected business pro ...
Six Sigma is a quality improvement methodology structured to reduce product or service failure rates to a negligible level. Six Sigma companies typically spend less than five percent of their revenues ...
Providing services with a high quality that are satisfying the requirements
Appling the specifications and legalizations to ensure the quality of service.
Best utilization of resources for continually improving the business activities.
CDGA keen to selects highly technical instructors based on professional field experience
Since CDGA was established, it considered a training partner for world class oil & gas institution
3012, Block 3, 30 Euro Business Park, Little Island, Co. Cork, T45 V220, Ireland
Mon to Fri 09:00 AM to 06:00 PM
Contact Us anytime!
Request Info