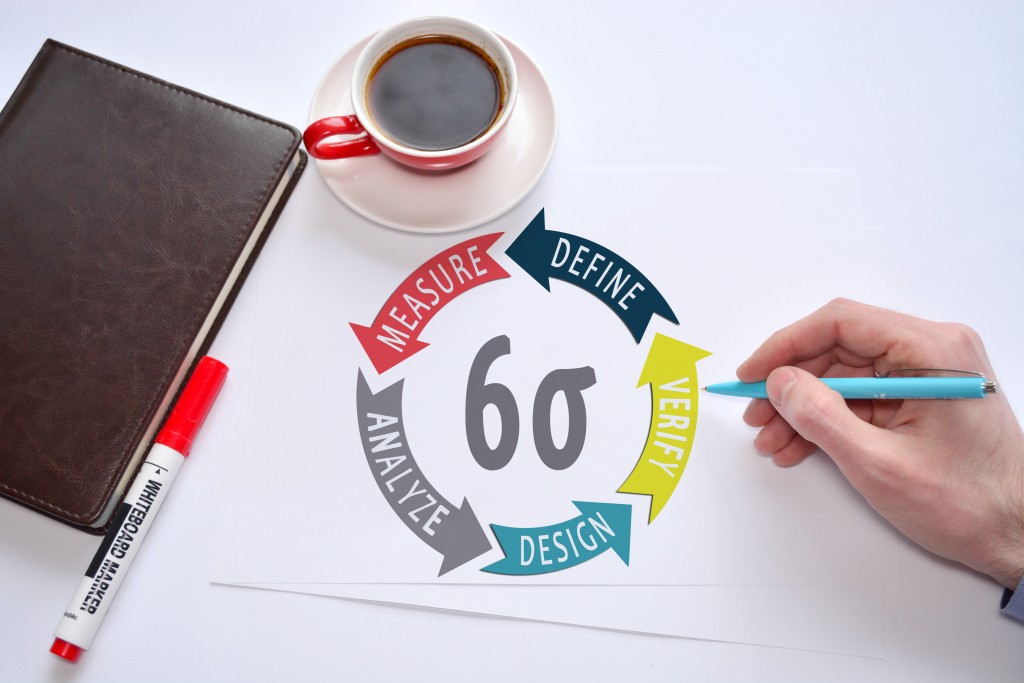
This course will teach and prepare individuals to implement the principles, practices, and techniques of Lean Six Sigma. Green belts traditionally lead process stakeholders and may also be assigned specific process level improvement projects to conduct on their own projects that normally do not require the statistical rigor demonstrated by a black belt.
By the end of this course delegates will be able to:
Quality Managers, Quality Assurance Engineers/Officials, Quality Engineers, Quality Improvement Professionals, Manufacturing/Process Engineers Project Managers, Corporate Managers, Executive Managers, Senior Managers, Middle Managers, Junior Managers, Human Resource Managers, Board of Directors, Entrepreneurs, Production Managers, Production Supervisors, Product Engineers, Inspectors, Line Leaders, Production Operators, Customer Service Professionals, Training Managers, Practitioners in the field of Quality Management, all those who are engaged in quality management implementation and improvement of organizational performance, those with an interest in quality management systems, those starting their career in quality management, staff who are involved in influencing, formulating or supporting the long term planning and strategy of the quality department or organization, as well as those who are responsible for linking, measuring and improving the performance of others, individuals from all organization departments including finance, quality and business operations staff functions as well as those who have direct intervention as process owners or stakeholders
Six Sigma Overview
Define Phase: Tools and Methods
Measure Phase: Introduction and Tools
Analyse Phase: Introduction and Tools
Improve Phase: Introduction and Tools
Control Phase: Introduction and Tools
Green Belt Project and Tollgate Review
Tips and tricks to get your project started
CDGA attendance certificate will be issued to all attendees completing minimum of 75% of the total course duration.
Code | Date | Venue | Fees | Register |
---|---|---|---|---|
QUA110-04 | 01-12-2025 | Kuala-Lumpur | USD 5950 |
Six Sigma is a quality philosophy, a process for improvement, a quality metric, and can be used to establish and reach aggressive goals, which are integrated with your company business and operating c ...
Engineering and Production Professionals all over the world are passionate about Six Sigma. Six Sigma is a methodology to develop great products and services that your customers love. Six Sigma is ...
Six Sigma is the comprehensive business improvement strategy made famous by organizations such as Motorola, General Electric, Honeywell and others, which has been used to generate significant improvem ...
Six Sigma is a quality improvement methodology structured to reduce product or service failure rates to a negligible level. Six Sigma companies typically spend less than five percent of their revenues ...
Providing services with a high quality that are satisfying the requirements
Appling the specifications and legalizations to ensure the quality of service.
Best utilization of resources for continually improving the business activities.
CDGA keen to selects highly technical instructors based on professional field experience
Since CDGA was established, it considered a training partner for world class oil & gas institution
3012, Block 3, 30 Euro Business Park, Little Island, Co. Cork, T45 V220, Ireland
Mon to Fri 09:00 AM to 06:00 PM
Contact Us anytime!
Request Info