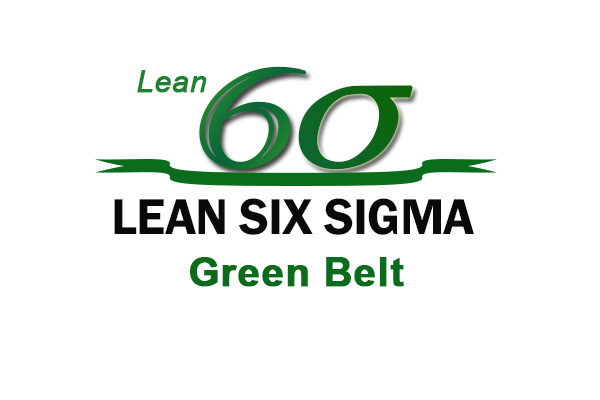
This course introduces participants to all of the core concepts underpinning the Lean Six Sigma approach to implementing a business improvement oriented culture and systems in organizations, and how these are used to improve customer satisfaction, process performance, and enhance competitive advantage and business results. In Lean Six Sigma organizations, it is the Green Belts who lead and contribute to the majority of improvement teams undertaking the improvement projects that will make continuous improvement through Lean Six Sigma a key element of achieving and maintaining operational excellence. The course will provide participants the level of knowledge and skill required to achieve accreditation at the Green Belt level.
By the end of this course delegates will be able to:
Quality Managers, Quality Assurance Engineers/Officials, Quality Engineers, Quality Improvement Professionals, Manufacturing/Process Engineers Project Managers, Corporate Managers, Executive Managers, Senior Managers, Middle Managers, Junior Managers, Human Resource Managers, Board of Directors, Entrepreneurs, Production Managers, Production Supervisors, Product Engineers, Inspectors, Line Leaders, Production Operators, Customer Service Professionals, Training Managers, Practitioners in the field of Quality Management, all those who are engaged in quality management implementation and improvement of organizational performance, those with an interest in quality management systems, those starting their career in quality management, staff who are involved in influencing, formulating or supporting the long term planning and strategy of the quality department or organization, as well as those who are responsible for linking, measuring and improving the performance of others
Introduction and Foundation Concepts
The Define Phase Detail
The Measure Phase Detail
The Measure Phase Detail (continued)
Understanding Variation
Assessing Process Performance
Measure Phase Tollgate Review
The Analyse Phase Detail 2
The Analyse Phase Detail 3
The Improve Phase Detail 1
The Improve Phase Detail 2
CDGA attendance certificate will be issued to all attendees completing minimum of 75% of the total course duration.
Code | Date | Venue | Fees | Register |
---|---|---|---|---|
QUA122-03 | 29-09-2025 | Kuala-Lumpur | USD 5950 | |
QUA122-04 | 23-11-2025 | Dubai | USD 5450 |
Six Sigma is a quality philosophy, a process for improvement, a quality metric, and can be used to establish and reach aggressive goals, which are integrated with your company business and operating c ...
Engineering and Production Professionals all over the world are passionate about Six Sigma. Six Sigma is a methodology to develop great products and services that your customers love. Six Sigma is ...
The Six Sigma methodology is a systematic application focused on achieving significant financial results and increasing customer satisfaction. When properly deployed on carefully selected business pro ...
Six Sigma is a quality improvement methodology structured to reduce product or service failure rates to a negligible level. Six Sigma companies typically spend less than five percent of their revenues ...
Providing services with a high quality that are satisfying the requirements
Appling the specifications and legalizations to ensure the quality of service.
Best utilization of resources for continually improving the business activities.
CDGA keen to selects highly technical instructors based on professional field experience
Since CDGA was established, it considered a training partner for world class oil & gas institution
3012, Block 3, 30 Euro Business Park, Little Island, Co. Cork, T45 V220, Ireland
Mon to Fri 09:00 AM to 06:00 PM
Contact Us anytime!
Request Info