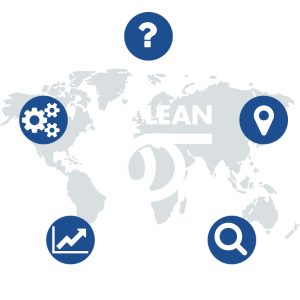
By the end of this course delegates will be able to:
OE champions, Maintenance managers, engineers & planners, reliability and maintenance engineers, facilities and utilities managers, top level maintenance technicians, operations and production managers & engineers, plant engineers, design engineers, reliability engineers & technicians, operators, safety engineers, risk engineers, CMMS and spare parts personnel, safety engineers and anyone who is involved.
Introduction to Lean
The Critical Lean Concepts
Lean Process Example
Introduction to Six Sigma
The Importance of Controlling Variation
Applying Six Sigma
Introducing Lean Six Sigma into Organizations
CDGA attendance certificate will be issued to all attendees completing minimum of 80% of the total course duration.
Code | Date | Venue | Fees | Register |
---|---|---|---|---|
MI146-03 | 07-09-2025 | Dubai | USD 5450 | |
MI146-04 | 23-11-2025 | Casablanca | USD 5950 |
This unique course is designed to merge the strategic and technical aspects of business management and analysis. Bringing together the MBA level business strategy toolkit with the Lean Six Sigma anal ...
The Six Sigma methodology is a systematic application focused on achieving significant financial results and increasing customer satisfaction. When properly deployed on carefully selected business pro ...
Six Sigma is the comprehensive business improvement strategy made famous by organizations such as Motorola, General Electric, Honeywell and others, which has been used to generate significant improvem ...
Providing services with a high quality that are satisfying the requirements
Appling the specifications and legalizations to ensure the quality of service.
Best utilization of resources for continually improving the business activities.
CDGA keen to selects highly technical instructors based on professional field experience
Since CDGA was established, it considered a training partner for world class oil & gas institution
3012, Block 3, 30 Euro Business Park, Little Island, Co. Cork, T45 V220, Ireland
Mon to Fri 09:00 AM to 06:00 PM
Contact Us anytime!
Request Info