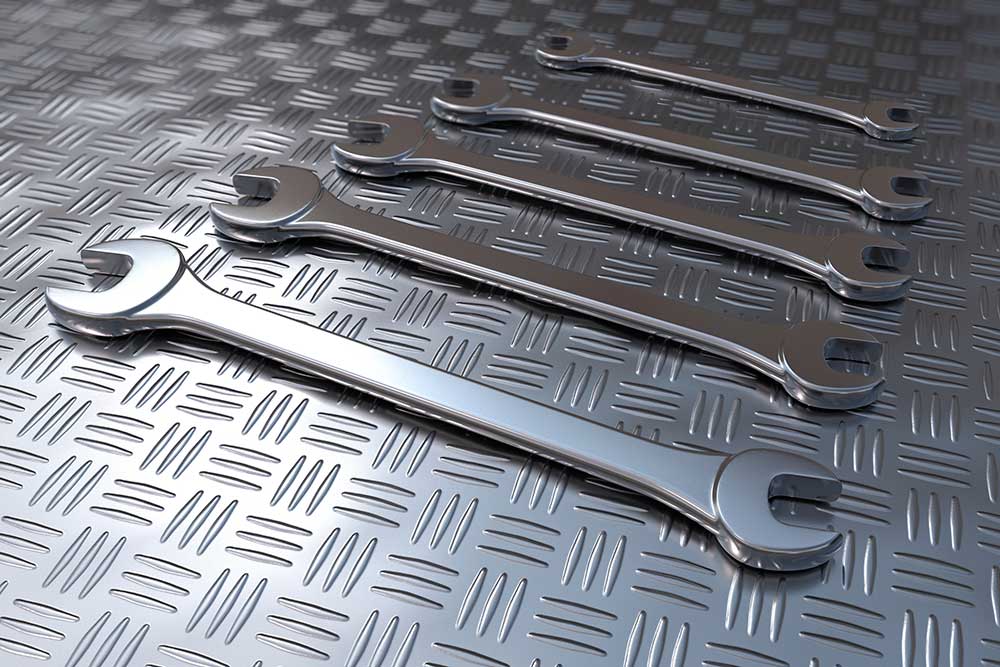
Participants gain a clear understanding of their role in defining and implementing cost effective maintenance policies and continuous improvement actions through an organisational development process based on either the TPM or RCM philosophy.
Delegates are the people in the organisation who are involved in, or dependent on, the development of an effective maintenance program and the people that take overall responsibility for the integrity of the physical assets.
Delegates include:
This interactive Training will be highly interactive, with opportunities to advance your opinions and ideas and will include;
DAY 1
The Changing World of Maintenance and Reliability Expectations
The Reality and Nature of Failure to Modern Equipment
Select Target Systems for Maintenance Program Optimisation
DAY 2
Define System Functions and Performance Requirements
Failure Modes, Effects and Risk Analysis
DAY 3
Maintenance Program Optimised Decision Making
Implementing RCM
Introduction to TPM
DAY 4
History and Evolution of Total Productive Maintenance
Productive Maintenance and Continuous Improvement
Equipment Effectiveness and OEE Equipment Defects and Losses
Problem Solving Techniques
Autonomous Maintenance
Predictive Maintenance Overview
TPM Implementation Strategies
DAY 5
Implementation Levels
Summary: RCM – TPM Selection Criteria, Implementation Implications
CDGA attendance certificate will be issued to all attendees completing minimum of 80% of the total course duration.
Code | Date | Venue | Fees | Register |
---|---|---|---|---|
MI222-03 | 12-10-2025 | Dubai | USD 5450 | |
MI222-04 | 07-12-2025 | Dubai | USD 5450 |
Reliability Centered Maintenance is a methodology used to determine the right maintenance tasks to ensure that any physical asset on system containing its uses want it to do, in its present operating ...
This course provides the fundamentals of Reliability-Centered Maintenance (RCM). The course is not process specific but gives the participant fundamental tools and knowledge required to participate in ...
Reliability Centered Maintenance (RCM) is commonly used to help establish safe minimum levels of maintenance, determine changes to operating procedures and help establish maintenance regimes and plans ...
Risk-Based Reliability Centered Maintenance (RCM) sets out to highlight and formalize the identification, categorization and management of risk as part of the development of failure management and mai ...
Total Productive Maintenance (TPM) is an equipment management program that emphasizes operator involvement and ownership of equipment performance. The goals of a TPM program are to maximize equipment ...
In today's manufacturing industries, more and more companies are seeking ways to improve their plant’s performance through the application of continuous improvement tools such as TPM. Although it orig ...
Providing services with a high quality that are satisfying the requirements
Appling the specifications and legalizations to ensure the quality of service.
Best utilization of resources for continually improving the business activities.
CDGA keen to selects highly technical instructors based on professional field experience
Since CDGA was established, it considered a training partner for world class oil & gas institution
3012, Block 3, 30 Euro Business Park, Little Island, Co. Cork, T45 V220, Ireland
Mon to Fri 09:00 AM to 06:00 PM
Contact Us anytime!
Request Info