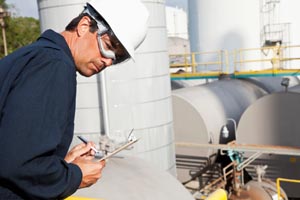
By the end of this course delegates will be able to:
Maintenance managers, maintenance supervisors, reliability and maintenance engineers, maintenance technicians, production managers, production supervisors, operators, plant engineers, and anyone who is involved in operating and maintaining of assets
Introduction to Maintenance Management
The Development of RCM
The Nature of Failures
The Meaning of Maintenance
Physical Asset Management
The RCM Process
CDGA attendance certificate will be issued to all attendees completing minimum of 80% of the total course duration.
Code | Date | Venue | Fees | Register |
---|---|---|---|---|
MI221-04 | 02-11-2025 | Casablanca | USD 5950 |
Reliability Centered Maintenance is a methodology used to determine the right maintenance tasks to ensure that any physical asset on system containing its uses want it to do, in its present operating ...
This course provides the fundamentals of Reliability-Centered Maintenance (RCM). The course is not process specific but gives the participant fundamental tools and knowledge required to participate in ...
Reliability Centered Maintenance (RCM) is commonly used to help establish safe minimum levels of maintenance, determine changes to operating procedures and help establish maintenance regimes and plans ...
Organisations invest huge sums of money in systems and processes to implement RCM or TPM, often with little understanding of what are the underlying philosophies of these programs. Each individual phi ...
Providing services with a high quality that are satisfying the requirements
Appling the specifications and legalizations to ensure the quality of service.
Best utilization of resources for continually improving the business activities.
CDGA keen to selects highly technical instructors based on professional field experience
Since CDGA was established, it considered a training partner for world class oil & gas institution
3012, Block 3, 30 Euro Business Park, Little Island, Co. Cork, T45 V220, Ireland
Mon to Fri 09:00 AM to 06:00 PM
Contact Us anytime!
Request Info