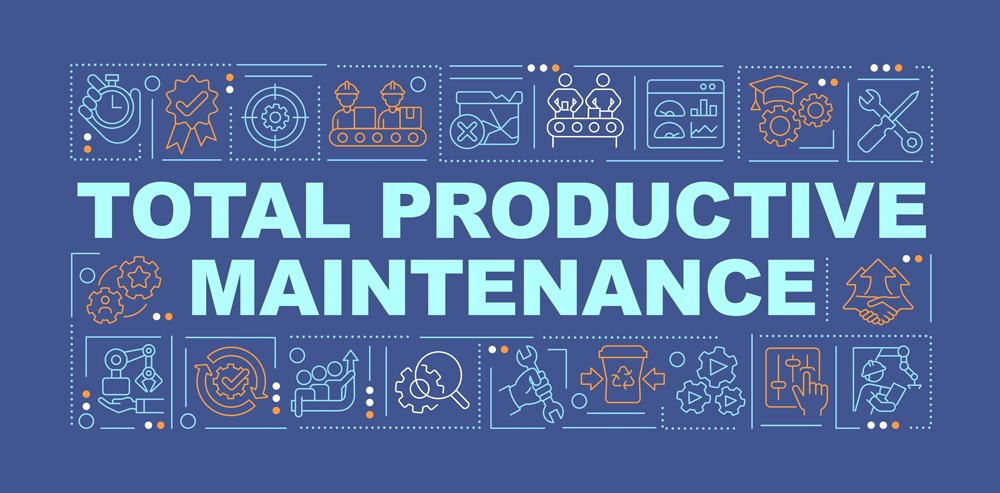
By the end of this course delegates will be able to:
OE champions, Maintenance managers, engineers & planners, reliability and maintenance engineers, facilities and utilities managers, top level maintenance technicians, operations and production managers & engineers, plant engineers, design engineers, reliability engineers & technicians, operators, safety engineers, risk engineers, CMMS and spare parts personnel, safety engineers and anyone who is involved in reliability engineering strategies or methodologies to include design engineers for capital projects engineers
What is TPM?
Equipment Lifetime Health
TPM and Its Operating Risk Reduction Benefits
Measuring Equipment Performance
The Importance of Operator Ownership of Equipment Performance
Getting Top Quality Equipment Performance
Requirements for Successful TPM Introduction
TPM Requires Change Management
A TPM Case Study
How to Approach Planning For TPM Introductions
CDGA attendance certificate will be issued to all attendees completing minimum of 80% of the total course duration.
Code | Date | Venue | Fees | Register |
---|---|---|---|---|
MI241-03 | 21-09-2025 | Cairo | USD 5450 | |
MI241-04 | 30-11-2025 | Dubai | USD 5450 |
Organisations invest huge sums of money in systems and processes to implement RCM or TPM, often with little understanding of what are the underlying philosophies of these programs. Each individual phi ...
In today's manufacturing industries, more and more companies are seeking ways to improve their plant’s performance through the application of continuous improvement tools such as TPM. Although it orig ...
Providing services with a high quality that are satisfying the requirements
Appling the specifications and legalizations to ensure the quality of service.
Best utilization of resources for continually improving the business activities.
CDGA keen to selects highly technical instructors based on professional field experience
Since CDGA was established, it considered a training partner for world class oil & gas institution
3012, Block 3, 30 Euro Business Park, Little Island, Co. Cork, T45 V220, Ireland
Mon to Fri 09:00 AM to 06:00 PM
Contact Us anytime!
Request Info