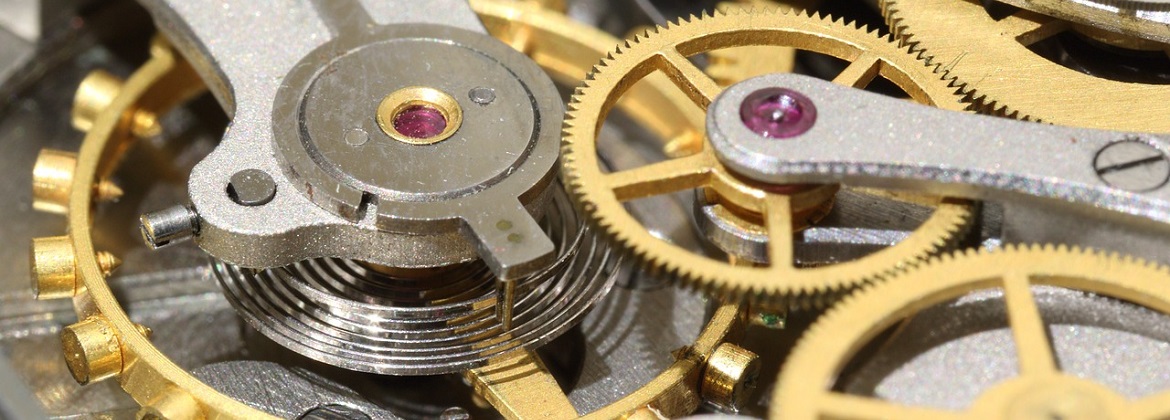
The training course will feature:
By the end of this course delegates will be able to:
Reliability Engineers, Maintenance Managers, Engineers & Planners, Reliability and Maintenance Engineers, Facilities and Utilities Managers, Design Engineers, Top Level Maintenance Technicians, OE Champions, Predictive and Preventive Maintenance, Technicians & Supervisors, Planners, Maintenance Supervisors, Crafts and Tradesmen, Operations Supervisors, Process Engineers, Inspectors and Inspection Supervisors, Equipment Engineers Team Leaders and Professionals in Maintenance, Engineering and Production, Maintenance managers, reliability and maintenance Engineers, Production Managers, Plant Engineers, Design Engineers, Reliability Engineers and Technicians, Operators, Safety Engineers, Risk Engineers, Safety Engineers and anyone who is involved in Reliability Engineering strategies or methodologies to include design engineers for capital projects engineers, Foreman and Technicians, Mechanical, Electrical and Operational Personnel, Personnel designated as Planners, Key leaders from each maintenance craft, Key operations personnel, Technical professionals responsible for maintenance and repair of equipment, Professionals involved in inspection and maintenance and repair, professionals involved in asset & maintenance management auditing, Quality & Compliance Managers, Lead Auditors & Audit Team Members, Process Controllers, Maintenance Supervisors, Maintenance Planners, Predictive Maintenance Technicians & Supervisors, Materials Management Managers and Supervisors, Service Company Representatives, Asset owners & Asset Managers
Physical Asset Management & Failure Analysis
Preventive Maintenance & Spare Parts Replacements
Equipment Inspection & Fitness for Service
Economics of Maintenance, Repair & Replacement
Total Productive Maintenance & Safety
KPI and OEE: Leading and Lagging Indicators
CDGA attendance certificate will be issued to all attendees completing minimum of 80% of the total course duration.
Code | Date | Venue | Fees | Register |
---|---|---|---|---|
MI187-03 | 19-10-2025 | Cairo | USD 5450 | |
MI187-04 | 21-12-2025 | Dubai | USD 5450 |
Maintenance Best Practices are critical for every successful individual and company. Maintenance is a unique business process. To be successfully managed, it requires an approach different from other ...
Not all of the plant facilities and equipment require high reliability; economically some components can be allowed to run to failure and a reasonable level of reliability is acceptable for other comp ...
This course is designed to teach the skills of availability engineering as detailed in the Facilities Maintenance Management Competency Map. As an intermediate level course we will use root cause fail ...
• Is your equipment (fixed or mobile) failing before planned replacement? • Are you unable to execute maintenance tasks because spare parts are not available? • Have you made significant investment ...
Providing services with a high quality that are satisfying the requirements
Appling the specifications and legalizations to ensure the quality of service.
Best utilization of resources for continually improving the business activities.
CDGA keen to selects highly technical instructors based on professional field experience
Since CDGA was established, it considered a training partner for world class oil & gas institution
3012, Block 3, 30 Euro Business Park, Little Island, Co. Cork, T45 V220, Ireland
Mon to Fri 09:00 AM to 06:00 PM
Contact Us anytime!
Request Info