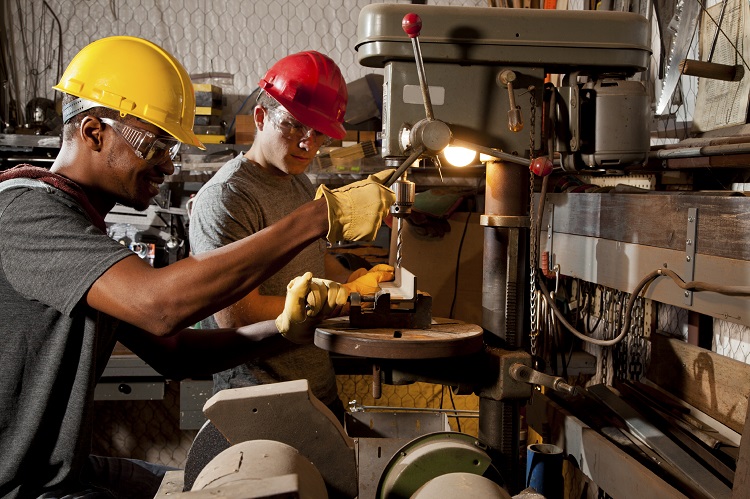
By the end of this course delegates will be able to:
Personnel involved in the maintenance of equipment and facilities including plant engineers, supervisors and managers; maintenance engineers, supervisors and managers; maintenance planners; property, facility managers who are responsible for ensuring that equipment and facilities operate in an economic and reliable fashion; consulting engineers; design engineers; industrial engineers; production and managers
Maintenance Philosophy and Strategy
Effective Maintenance Practices
Maintenance Staffing
Efficiently Applying Reliability Cantered Maintenance
Maintenance Planning and Scheduling
General Maintenance Information
Monitoring and Reporting Maintenance Activities
Effectively Managing Maintenance Work
CDGA attendance certificate will be issued to all attendees completing minimum of 80% of the total course duration.
Code | Date | Venue | Fees | Register |
---|---|---|---|---|
MI185-04 | 23-11-2025 | Dubai | USD 5450 |
Maintenance Best Practices are critical for every successful individual and company. Maintenance is a unique business process. To be successfully managed, it requires an approach different from other ...
This course is designed to teach the skills of availability engineering as detailed in the Facilities Maintenance Management Competency Map. As an intermediate level course we will use root cause fail ...
Major world companies from the process and petrochemical industry have developed their maintenance practices based on the optimization of predictive maintenance management system. This approach works ...
• Is your equipment (fixed or mobile) failing before planned replacement? • Are you unable to execute maintenance tasks because spare parts are not available? • Have you made significant investment ...
Providing services with a high quality that are satisfying the requirements
Appling the specifications and legalizations to ensure the quality of service.
Best utilization of resources for continually improving the business activities.
CDGA keen to selects highly technical instructors based on professional field experience
Since CDGA was established, it considered a training partner for world class oil & gas institution
3012, Block 3, 30 Euro Business Park, Little Island, Co. Cork, T45 V220, Ireland
Mon to Fri 09:00 AM to 06:00 PM
Contact Us anytime!
Request Info