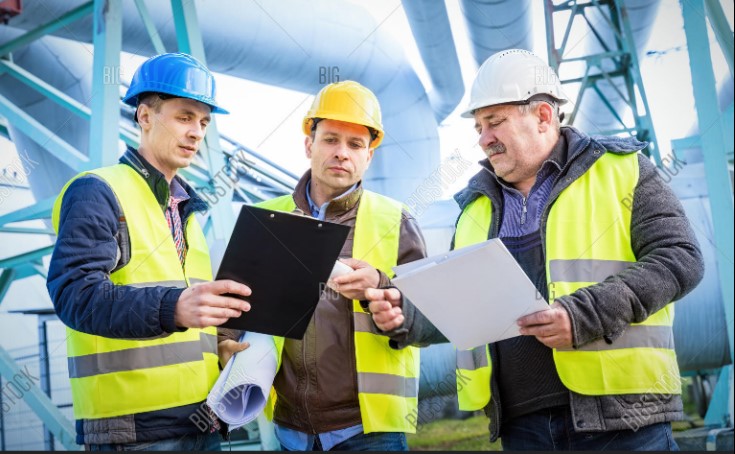
A well prepared MTA would provide critical input to support and address the needs other ILS elements, such as training and technical publications development. The technical publication would utilize data such as the detailed task description, which also provide valuable input for the development of maintenance training courses and support material.
A highly interactive combination of lectures and discussion sessions will be managed to maximize the amount and quality of information and knowledge transfer. The sessions will start by raising the most relevant questions, and motivate everybody find the right answers. The delegates will also be encouraged to raise their own questions and to share in the development of the right answers using their own analysis and experiences. Tests of multiple-choice type will be made available on daily basis to examine the effectiveness of delivering the course
Day 1
INTRODUCTION
Effective maintenance Management
The Maintenance Task Analysis (MTA)
Introduction
Task analysis
Hierarchical Task Analysis
Identifying each step of the repair process
Understanding the Task Requirements
Day 2
MTA Description and Investigation Resources
Day 3
Corrective Maintenance Task Generation Supportability Analysis Staffing Optimization
MAT output
Day 4
Day 5
Building a system for equipment condition indicating
Failure and maintenance notations
Failure descriptors
Failure causes
Method of detection
Case Studies, Group Discussions, Last Day Review, Assessments will be carried out
CDGA attendance certificate will be issued to all attendees completing minimum of 80% of the total course duration.
Code | Date | Venue | Fees | Register |
---|---|---|---|---|
MI171-03 | 24-08-2025 | Cairo | USD 5450 | |
MI171-04 | 23-11-2025 | Dubai | USD 5450 |
Time management skills are indispensable to the personal development tool kit. This course will help participants to improve their skills, in terms of work and personal life. It will enable them to ma ...
High plant reliability is critical for every successful company, and it has never been more important than it is in the present economic climate. The costs associated with equipment downtime and redu ...
The course explains basic vibration theory, the benefits of predictive maintenance and how to organize a predictive maintenance program. Coupled with this will be an overview of the interdependence of ...
Providing services with a high quality that are satisfying the requirements
Appling the specifications and legalizations to ensure the quality of service.
Best utilization of resources for continually improving the business activities.
CDGA keen to selects highly technical instructors based on professional field experience
Since CDGA was established, it considered a training partner for world class oil & gas institution
3012, Block 3, 30 Euro Business Park, Little Island, Co. Cork, T45 V220, Ireland
Mon to Fri 09:00 AM to 06:00 PM
Contact Us anytime!
Request Info