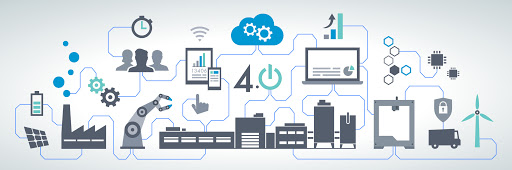
Pre-Requisite:
This is a specialist analytical and modelling programme that is designed for specialists in technical maintenance. It involves extensive statistical analysis and data modelling methods. Attendees need to be computer literate, familiar with and competent at using Microsoft Excel, and must have technical backgrounds, ideally to degree standard in an engineering or related technical subject.
It is highly recommended to Reliability Engineers, Maintenance Planners, Maintenance Supervisors and Maintenance Engineers
DAY 1 - Maintenance strategies and the power of historical data
DAY 2 - Statistical analysis of failure data
DAY 3 - Reliability models and approaches to modelling
DAY 4 - Cost based maintenance and the basis of a reliability toolbox
DAY 5 - The finalisation of a comprehensive reliability toolbox in Excel
CDGA attendance certificate will be issued to all attendees completing minimum of 80% of the total course duration.
Code | Date | Venue | Fees | Register |
---|---|---|---|---|
MI194-03 | 05-10-2025 | Dubai | USD 5450 | |
MI194-04 | 07-12-2025 | Cairo | USD 5450 |
MTA is the identification of the steps, spares and materials, tools, support equipment, personnel skill levels as well as any facility issues that must be considered for a given repair task. Also incl ...
Maintenance & reliability best practices are critical for every successful individual and company. This course delivers many practical and new maintenance and reliability best practices concepts and t ...
Industrial processes today operate on very large scales with the advent of modern industrial plants. Such plants sometimes operate hundreds of equipment, not to mention thousands of instruments for th ...
Providing services with a high quality that are satisfying the requirements
Appling the specifications and legalizations to ensure the quality of service.
Best utilization of resources for continually improving the business activities.
CDGA keen to selects highly technical instructors based on professional field experience
Since CDGA was established, it considered a training partner for world class oil & gas institution
3012, Block 3, 30 Euro Business Park, Little Island, Co. Cork, T45 V220, Ireland
Mon to Fri 09:00 AM to 06:00 PM
Contact Us anytime!
Request Info