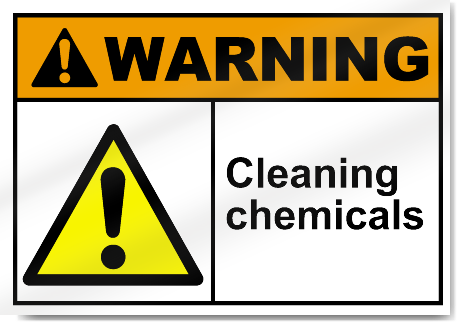
An advanced course to develop the engineers and operators deals with Materials and Corrosion Control about:
This interactive Training will be highly interactive, with opportunities to advance your opinions and ideas and will include;
CDGA attendance certificate will be issued to all attendees completing minimum of 80% of the total course duration.
Code | Date | Venue | Fees | Register |
---|---|---|---|---|
PE121-03 | 12-10-2025 | Dubai | USD 5450 | |
PE121-04 | 07-12-2025 | Dubai | USD 5450 |
This course will provide comprehensive coverage of all chemical EOR processes. The course materials are based on the instructor’s hands-on experience, personal collection of field cases and learning, ...
Nowadays, membrane technologies are becoming more frequently used for separation of wide varying mixtures in the petrochemical-related industries and can compete successfully with traditional schemes. ...
Chemical engineering is at the heart of much of the chemical, oil, gas, and petrochemical industries. The chemical engineer is interested in the transportation and transformation of solids, liquids an ...
Providing services with a high quality that are satisfying the requirements
Appling the specifications and legalizations to ensure the quality of service.
Best utilization of resources for continually improving the business activities.
CDGA keen to selects highly technical instructors based on professional field experience
Since CDGA was established, it considered a training partner for world class oil & gas institution
3012, Block 3, 30 Euro Business Park, Little Island, Co. Cork, T45 V220, Ireland
Mon to Fri 09:00 AM to 06:00 PM
Contact Us anytime!
Request Info