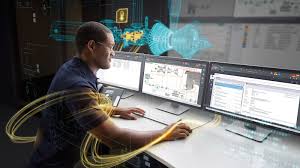
Upon the successful completion of this course, participants will be able to:
PRE-TEST
Introduction
Petroleum Properties & Definitions
Development of Process Data
Equipment Sizing, Selection and Design Process Equipment Categories
Piping
Pumps
Compressors
Heat Exchangers / Air Coolers
Direct-Fired Heaters
Process Vessels
Fractionators Columns
Reactors
Ancillary Equipment
Mechanical & Safety Aspects
Process Control
Materials of Construction
Process Risk Analysis
Cost Estimating
Process Design Specifications
Q & A Discussion
POST-TEST
CDGA attendance certificate will be issued to all attendees completing minimum of 75% of the total course duration.
Code | Date | Venue | Fees | Register |
---|---|---|---|---|
PE106-03 | 21-09-2025 | Casablanca | USD 5950 | |
PE106-04 | 30-11-2025 | Dubai | USD 5450 |
This seminar will enable delegates to remain abreast of the latest researched trends, techniques and strategies to improve the condition and performance of their operational process. This hands-on int ...
Providing services with a high quality that are satisfying the requirements
Appling the specifications and legalizations to ensure the quality of service.
Best utilization of resources for continually improving the business activities.
CDGA keen to selects highly technical instructors based on professional field experience
Since CDGA was established, it considered a training partner for world class oil & gas institution
3012, Block 3, 30 Euro Business Park, Little Island, Co. Cork, T45 V220, Ireland
Mon to Fri 09:00 AM to 06:00 PM
Contact Us anytime!
Request Info