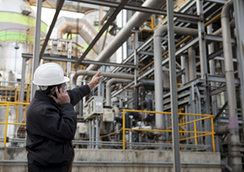
By the end of this course delegates will learn about:
Corrosion Control Engineers & Personnel, Process Engineers, Metallurgists, Inspection Personnel, Mechanical Engineers, Material Selection Personnel, Plant Contractors, Operations Engineers, Team Leaders & Supervisors, Maintenance Engineers, Maintenance Supervisors, Senior Plant Supervisors, Mechanical Engineers, Corrosion Control & Monitoring Systems Personnel, Equipment Engineers, Maintenance Engineers and Planners, Team Leaders, Managers & Coordinators, Construction Coordinators,Technologists, Safety Officers, Maintenance Team Leaders & Engineers, Design Engineers, Service Company Representatives, Oil and Gas Production Facilities Personnel, Chemists, Chemical Engineers, Inspectors and Inspection Engineers & Supervisors, Technicians and Supervisors, Environmental Specialists, New Petroleum Engineers, Asset Management Personnel, Construction Engineers, Refinery Chemists, Chemical Engineers, Personnel who are / will be responsible for detecting, inspecting, monitoring, controlling corrosion in oil and gas piping, pipelines used in production operations and Personnel responsible for metallurgy, corrosion or the prevention of failures in plant and equipment
CDGA attendance certificate will be issued to all attendees completing minimum of 80% of the total course duration
Code | Date | Venue | Fees | Register |
---|---|---|---|---|
FAC133-03 | 12-10-2025 | Dubai | USD 5450 | |
FAC133-04 | 07-12-2025 | Casablanca | USD 5950 |
This course presents a history of metals and the background on the origins of various metals. It provides an explanation of physical characteristics of metals, including the reason metals behave diffe ...
This training course is designed to give a semi-detailed discussion of Metallurgical failure analysis in order for the course material to suit participants with or without a metallurgical background. ...
Providing services with a high quality that are satisfying the requirements
Appling the specifications and legalizations to ensure the quality of service.
Best utilization of resources for continually improving the business activities.
CDGA keen to selects highly technical instructors based on professional field experience
Since CDGA was established, it considered a training partner for world class oil & gas institution
3012, Block 3, 30 Euro Business Park, Little Island, Co. Cork, T45 V220, Ireland
Mon to Fri 09:00 AM to 06:00 PM
Contact Us anytime!
Request Info