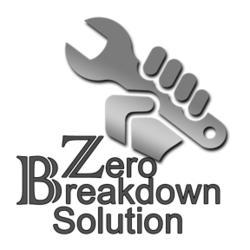
By the end of this course delegates will be able to:
OE champions, Maintenance managers, engineers & planners, reliability and maintenance engineers, facilities and utilities managers, top level maintenance technicians, operations and production managers & engineers, plant engineers, design engineers, reliability engineers & technicians, operators, safety engineers, risk engineers, CMMS and spare parts personnel, safety engineers and anyone who is involved in reliability engineering.
Limitations of Machines and Materials
Determining the Reliability of Parts
Reliability of Complex Parts
Reliability Prediction
Reliability of Machines
Instilling Reliability Principles into Maintenance
Introduction to Profit Centered Maintenance
Maintenance Strategy Choices
Selecting Maintenance to Deliver Reliability
Maintenance: Risk Management Strategy
Improving Maintenance & Reliability Results
Maximum Life Cycle Profit Maintenance
Managing Risk in Your Business and Operations
Precision Maintenance & Precision Practices for Failure-Free Operation
Getting Operators to Drive Equipment Reliability
Modernize, Systematize & Standardize Your Maintenance Processes
CDGA attendance certificate will be issued to all attendees completing minimum of 80% of the total course duration.
Code | Date | Venue | Fees | Register |
---|---|---|---|---|
MI249-03 | 12-10-2025 | Dubai | USD 5450 | |
MI249-04 | 21-12-2025 | Casablanca | USD 5950 |
Root cause analysis (RCA) is a class of problem solving methods aimed at identifying the root causes of problems or events. The practice of RCA is predicated on the belief that problems are best solve ...
Machines deteriorate as they get older so we can expect a certain amount of performance falloff and general deterioration of the machine. If we understand the failure mechanisms that are in place we c ...
Maintenance & Reliability Best Practices are critical for every successful individual and company. The first module of this training course delivers many practical and new Maintenance and Reliability ...
This course is packed with the insights and the powerful techniques of successful maintenance planning and scheduling for high equipment reliability. The comprehensive content gives you best practice ...
Providing services with a high quality that are satisfying the requirements
Appling the specifications and legalizations to ensure the quality of service.
Best utilization of resources for continually improving the business activities.
CDGA keen to selects highly technical instructors based on professional field experience
Since CDGA was established, it considered a training partner for world class oil & gas institution
3012, Block 3, 30 Euro Business Park, Little Island, Co. Cork, T45 V220, Ireland
Mon to Fri 09:00 AM to 06:00 PM
Contact Us anytime!
Request Info