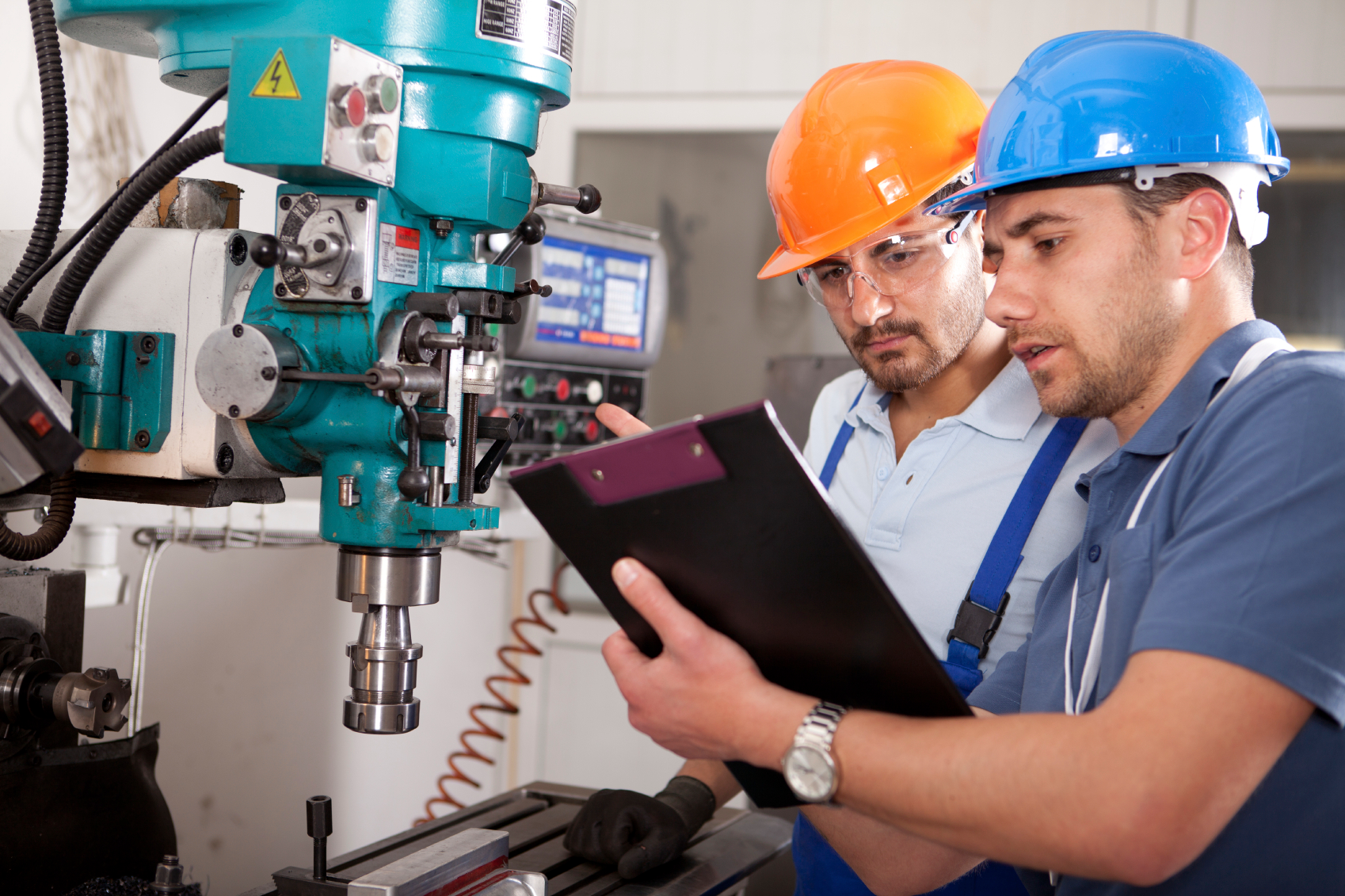
Machines deteriorate as they get older so we can expect a certain amount of performance fall off and general deterioration of the machine. If we understand the failure mechanisms that are in place we can identify which parameters best indicate the deterioration of the machine. In this comprehensive course the delegates will benefit from using modern methods & technologies to learn reliability basics, fault analysis and monitoring techniques . Failure analysis and Predictive Maintenance techniques, including vibration analysis, are discussed in the course with a view to optimising the maintenance engineering effort while maximising production. Other techniques that will be addressed include infrared thermography, passive ultrasonics, tribology and performance monitoring.
At the end of this seminar participants will have:
An understanding of Machine Failure Analysis techniques.
An understanding of why machines fail and how to identify the “bad actors”.
An understanding of a range of Predictive Maintenance Technologies .
Knowledge of the potential contribution of each these technologies to maintenance efficiency .
Guidelines indicating how these technologies can interact with and support each other
Hints and Tips for practical application of these technologies so as to achieve the best results .
A practical approach to developing an action plan to utilize these technologies in their own areas of responsibility, fitting them into the overall maintenance strategy, and measuring benefits strategy, and measuring benefits.
This course towards Supervisors, Team Leaders and Managers in Maintenance, Engineering and Production. The course also benefit anyone who wishes to update themselves on Predictive Maintenance Technologies and Failure Analysis techniques, as well as those who have to judge the suitability of these technologies for their needs, and learn how to implement them for the benefit of their organizations.
The Following Topics will be covered in this course over five days Outlines:
Day 1
An introduction to Reliability
o Rotating Machines
• Centrifugal pumps
• Centrifugal & rotary compressors. Fans & blowers
• Drivers – turbines and motors
• Common problems on rotating machines
• Performance deterioration
• Vibration as an indicator
• Failure of function
• Economics of maintenance engineering
• Maintenance & asset management
o Equipment Reliability
• Reliability in design
• Specifications & application
• Operational reliability, including first line maintenance and TPM
• Maintenance reliability, including Maintenance Planning and Management
• Maintenance strategies and their implementation
1- Root cause failure analysis
• Introduction
• Failure Analysis (FA)
• Root Cause Failure Analysis (RCFA)
• Root Cause Analysis (RCA)
• general analysis techniques
• Brainstorming
• Brainstorming guidelines
• Case stud
Day 2
2- Root cause failure analysis methodology
• 5Why
• Barrier Analysis
• Change Analysis
• Causal Factor Tree Analysis
• Failure mode and effects analysis
• Fish-Bone Diagram or Ishikawa diagram
• Pareto Analysis
• Fault Tree Analysis
Day 3
3- safety related issue
4-process performance
5-Define the problem.
6-Gather data/evidence.
7 -Identify issues that contributed to the problem.
8-Find root causes.
9-Develop solution recommendations.
10-Implement the solutions
• Case studies
Day 4
Machine Failure Analysis
• Understanding fault causes
• Diagnosis of fatigue mechanisms – mechanical & thermal
• Bearings
• Bearing types & application
• Plain & pad bearings - hydrodynamic lubrication, failure types and identification
• Rolling element bearings – elastohydrodynamic lubrication, failure types and identification
• Pump & compressors seals
• Construction.
• Application
• Failures types – identification and analysis
• Trouble shooting techniques
• Field trouble shooting
• Engineering trouble shooting – problem solving
• Case studies
Day 5
Condition Monitoring & Predictive Maintenance
Predictive Maintenance Concepts
• Predictive Maintenance – background and history
• Predictive Maintenance Technologies – an overview
• Potential Failure Analysis – deciding which technologies to apply
• On Line or Off line
• Protection systems
• Monitoring systems
• Analytical systems
• vibration Analysis
• Infrared Thermography
• Thermographic applications
• Passive Ultrasonics - contact and non-contact
• Ultrasonic Applications
• Tribology – oil analysis
• Case studies
CDGA attendance certificate will be issued to all attendees completing minimum of 80% of the total course duration.
Code | Date | Venue | Fees | Register |
---|---|---|---|---|
MI227-03 | 28-09-2025 | Dubai | USD 5450 | |
MI227-04 | 16-11-2025 | Cairo | USD 5450 |
Health and safety technology and procedures are very important aspects of health and safety management. However, on their own, these will not provide a continuous improvement in health and safety and ...
In this 5-day course, participants will gain a strong technical and practical understanding of bearing design features and implications of many bearings types. This course will provide the participant ...
RCA is an approach for identifying non-conformance underlying causes of why an incident occurred so that the most effective solutions can be identified and implemented. It's typically used when someth ...
Most organizations have accident investigation procedures. However, these procedures are often based on a blame culture & do not inspire the investigator to ND & correct the defects in the management ...
Providing services with a high quality that are satisfying the requirements
Appling the specifications and legalizations to ensure the quality of service.
Best utilization of resources for continually improving the business activities.
CDGA keen to selects highly technical instructors based on professional field experience
Since CDGA was established, it considered a training partner for world class oil & gas institution
3012, Block 3, 30 Euro Business Park, Little Island, Co. Cork, T45 V220, Ireland
Mon to Fri 09:00 AM to 06:00 PM
Contact Us anytime!
Request Info