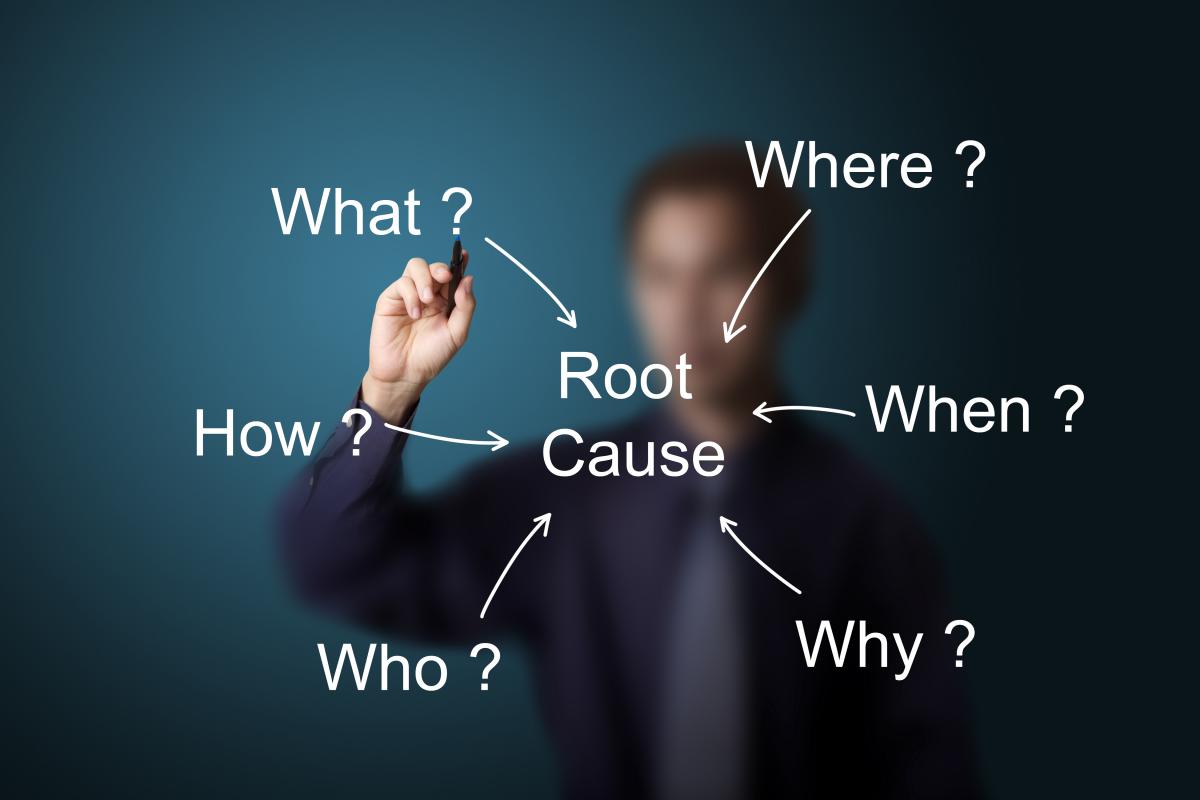
The primary objective of this course is to recognize the value of conducting proper root cause analysis and documenting failure investigations. Emphasis is placed on the application and practical, hands-on aspects of how to facilitate root cause analysis. Additionally, the course will provide candidates with the principles and techniques involved in identifying failures and deviations, categorizing problems, assigning responsibility and tracking team activities. This course is designed to teach the attendee how to use three of the most popular and useful problem solving techniques available today and Five Whys, Logic Trees, and Causal Factor Mapping. Class lecture will be reinforced with numerous practice opportunities, so the attendee will feel comfortable going back to the job and attacking chronic plant problems and incidents right away.
By the end of this course delegates will be able to:
Craft, first line supervisors, engineers, reliability and maintenance engineers, and managers who may participate in root cause analysis investigations of chronic equipment problems, or serious incidents related to the environment or safety. Upper level managers who want to understand how rigorously applying Root Cause Analysis techniques can bolster bottom line results should also attend.
CDGA attendance certificate will be issued to all attendees completing minimum of 80% of the total course duration.
Code | Date | Venue | Fees | Register |
---|---|---|---|---|
MI226-03 | 12-10-2025 | Casablanca | USD 5950 | |
MI226-04 | 30-11-2025 | Dubai | USD 5450 |
Root cause analysis (RCA) is a class of problem solving methods aimed at identifying the root causes of problems or events. The practice of RCA is predicated on the belief that problems are best solve ...
Health and safety technology and procedures are very important aspects of health and safety management. However, on their own, these will not provide a continuous improvement in health and safety and ...
Most organizations have accident investigation procedures. However, these procedures are often based on a blame culture & do not inspire the investigator to ND & correct the defects in the management ...
Root cause analysis (RCA) is a class of problem solving methods aimed at identifying the root causes of problems or events. The practice of RCA is predicated on the belief that problems are best solve ...
In this 5-day course, participants will gain a strong technical and practical understanding of bearing design features and implications of many bearings types. This course will provide the participant ...
Providing services with a high quality that are satisfying the requirements
Appling the specifications and legalizations to ensure the quality of service.
Best utilization of resources for continually improving the business activities.
CDGA keen to selects highly technical instructors based on professional field experience
Since CDGA was established, it considered a training partner for world class oil & gas institution
3012, Block 3, 30 Euro Business Park, Little Island, Co. Cork, T45 V220, Ireland
Mon to Fri 09:00 AM to 06:00 PM
Contact Us anytime!
Request Info