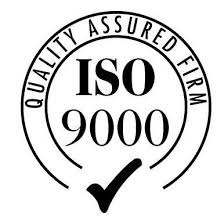
There are many standards in the ISO 9000 family, including:
By the end of this course delegates will be able to:
Executives, engineers, and supervisors from QA, production, maintenance and engineering, Managers, Supervisors, Engineers, Practitioners in the field of Quality Management, Quality Engineering, Continuous improvement, production & operation and all parties associated with process quality, improvement, production and operation of the company or organization
CDGA attendance certificate will be issued to all attendees completing minimum of 75% of the total course duration.
Code | Date | Venue | Fees | Register |
---|---|---|---|---|
QUA107-03 | 20-10-2025 | Istanbul | USD 5950 | |
QUA107-04 | 21-12-2025 | Dubai | USD 5450 |
Many organizations all-over the world have used the ISO 9001 quality management system standard as a framework for managing quality assurance within their operations and meeting the expectations of th ...
Measurement in testing laboratory is needed by quality control services. Testing is made using measurement equipment based validated methods and standards. It is usually used some known parameters cha ...
Providing services with a high quality that are satisfying the requirements
Appling the specifications and legalizations to ensure the quality of service.
Best utilization of resources for continually improving the business activities.
CDGA keen to selects highly technical instructors based on professional field experience
Since CDGA was established, it considered a training partner for world class oil & gas institution
3012, Block 3, 30 Euro Business Park, Little Island, Co. Cork, T45 V220, Ireland
Mon to Fri 09:00 AM to 06:00 PM
Contact Us anytime!
Request Info