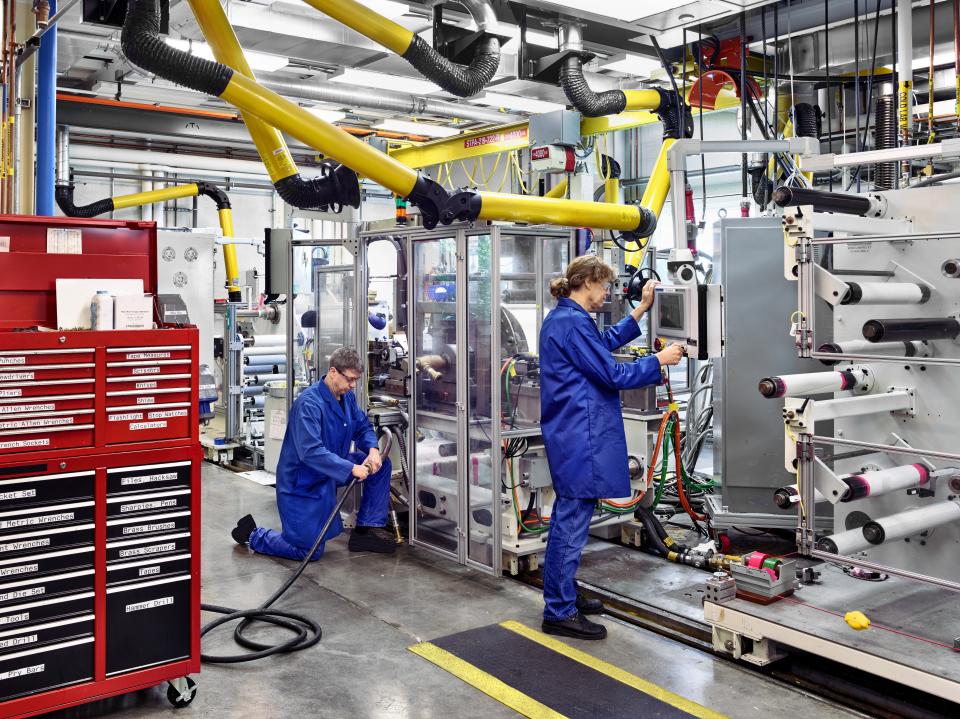
By the end of this course delegates will be able to:
Analyze engineering failures critically in a given design by considering all possible failure mechanisms (sometimes, these failure mechanisms may be competing with one another
Understanding Failures
Failure Mechanics
Failure Prevention by Design
Avoiding Failures
Understanding Planned Maintenances
Using Predictive Maintenance
Inspection, Assessment and Maintenance
Control Mechanisms
CDGA attendance certificate will be issued to all attendees completing minimum of 80% of the total course duration.
Code | Date | Venue | Fees | Register |
---|---|---|---|---|
ME122-03 | 19-10-2025 | Cairo | USD 5450 | |
ME122-04 | 07-12-2025 | Dubai | USD 5450 |
The possible reasons leading to machinery failure is important to personnel involved to machinery, operation and maintenance. This will help all of them to take possible precessions in their jobs to a ...
This 5-day workshop is designed to provide excellent understanding on both a theoretical and practical level to attendees. The workshop starts at a basic level, to ease the engineer and technician int ...
Excellent Troubleshooting skills are considered a core competency for 'Best-in-Class' industrial companies. If your company’s goals include minimizing downtime then
Providing services with a high quality that are satisfying the requirements
Appling the specifications and legalizations to ensure the quality of service.
Best utilization of resources for continually improving the business activities.
CDGA keen to selects highly technical instructors based on professional field experience
Since CDGA was established, it considered a training partner for world class oil & gas institution
3012, Block 3, 30 Euro Business Park, Little Island, Co. Cork, T45 V220, Ireland
Mon to Fri 09:00 AM to 06:00 PM
Contact Us anytime!
Request Info