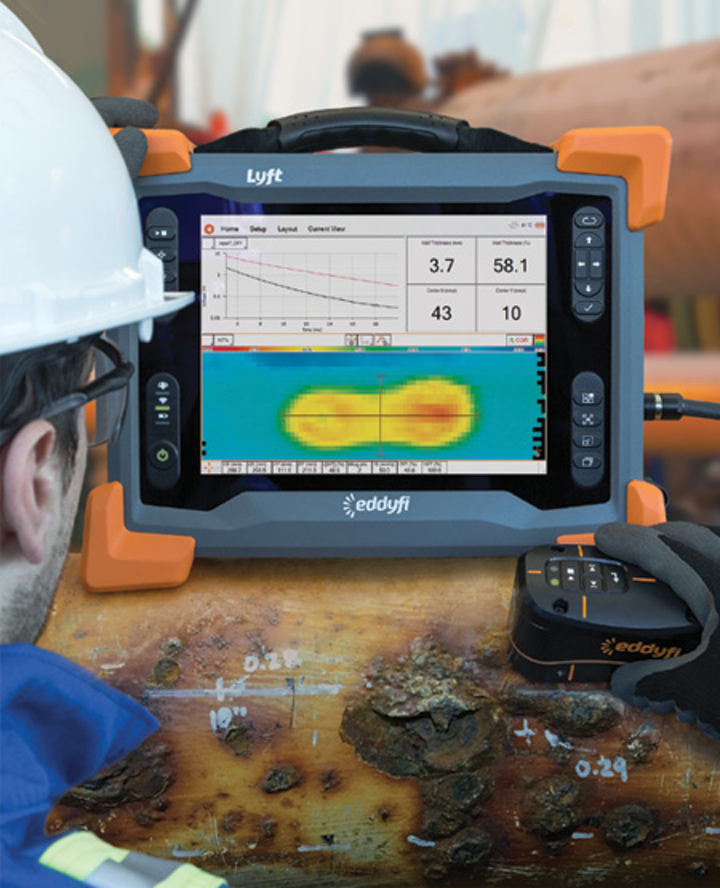
Upon completion of this course, you will gain an understanding of corrosion engineering in oil and gas production involving the various methods available for corrosion control, regulatory and safety matters, and the contribution of an integrated monitoring and inspection programme for operations and diagnosis of problems.
The course is designed essentially for process and mechanical engineers employed by the operating companies engaged in oil and gas production. The material is also appropriate for those personnel concerned with specialist functions in the oil industry including inspection, material selection, and corrosion control, as well as those involved in R&D.
Staff of service companies providing corrosion inhibitors and overall corrosion services should also find this course beneficial, together with companies or manufacturers marketing materials, coatings and equipment for cathodic protection, inspection (NDT) and corrosion monitoring.
This interactive Training will be highly interactive, with opportunities to advance your opinions and ideas and will include;
Overview – Corrosion in Oil and Gas Production
Economics of Corrosion Damage:
Introduction to Corrosion and Corrosion Control:
Basic Corrosion Principles:
Forms of Corrosion:
Corrosion Aspects – Oxygen:
Corrosion Aspects – Sour:
Corrosion Aspects – Sweet:
Corrosion Aspects – Bacterial:
Corrosion Prevention – Inhibitors:
Corrosion Prevention – Design:
Corrosion Prevention – Cathodic Protection:
Corrosion Prevention – Materials and Selection:
Corrosion Prevention – Coatings and Linings:
Corrosion Monitoring:
Water Chemistry:
Manufacturers’ Demonstration:
Inspection and Nondestructive testing (NDT):
Failure Analysis:
Pipelines and Risers:
Oil Treatment Corrosion:
Case Histories Workshop
Sweetening Processes –Corrosion
Quality Assurance:
Subsea Systems – Corrosion:
Case History – Oil Storage Tank Corrosion
Oilfield and Oil Treating Facilities:
CDGA Consultant certificate will be issued to all attendees completing minimum of 75% of the total tuition hours of the course.
Code | Date | Venue | Fees | Register |
---|---|---|---|---|
PE128-03 | 05-10-2025 | Dubai | USD 5450 | |
PE128-04 | 07-12-2025 | Cairo | USD 5450 | |
PE128-05 | 14-12-2025 | Dubai | USD 5450 |
Corrosion problems have always presented a severe challenge to oil and gas producing operations. Operators plan for long periods of continuous production with maintenance schedules for the prescribed ...
This comprehensive corrosion course consists of several modules covering virtually every aspect of corrosion. The course is structured in a flexible modular format so that beginners will establish a s ...
Providing services with a high quality that are satisfying the requirements
Appling the specifications and legalizations to ensure the quality of service.
Best utilization of resources for continually improving the business activities.
CDGA keen to selects highly technical instructors based on professional field experience
Since CDGA was established, it considered a training partner for world class oil & gas institution
3012, Block 3, 30 Euro Business Park, Little Island, Co. Cork, T45 V220, Ireland
Mon to Fri 09:00 AM to 06:00 PM
Contact Us anytime!
Request Info