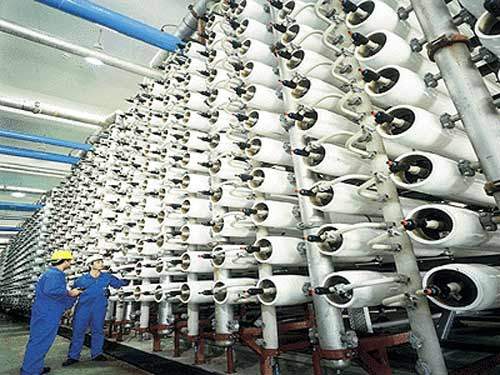
After successful completion of the course delegates will have an excellent knowledge RO plant O & M, troubleshooting, design and components’ selection, chemical cleaning and RO economics.
Plant & technical support managers, O & M supervisors, senior mechanical and electrical engineers, senior chemists, environmental and consulting engineers for reverse osmosis plants.
You will gain valuable know-how related to reverse osmosis plants on:
Contents: |
Part I: Membrane Modules Configuration:
Part II: RO System Configuration and Design Parameters
Part III: Reverse Osmosis System Operation and Maintenance
Part IV: RO Engineering Design Process
Part V: Corrosion Introduction
Part VI: Technical
Part VII: Maintenance
Part VIII: Administrative
Part IX: Safety
Part X: Troubleshooting Spiral Wound RO & NF Systems
Part XI: Cleaning RO and NF Membrane Elements
SUMMERY AND CLOSING
CDGA attendance certificate will be issued to all attendees completing minimum of 75% of the total course duration.
Code | Date | Venue | Fees | Register |
---|---|---|---|---|
PE103-03 | 19-10-2025 | Casablanca | USD 5950 | |
PE103-04 | 07-12-2025 | Amman | USD 5450 |
Start Up and Commissioning of new plant and equipment presents both a major technical and management challenge. An organization’s personnel must familiarise themselves with new equipment, processes an ...
Designing process plants is a complex and demanding process. The design of plant layout is one of the most important tasks before plant construction. A successful plant layout will not only reduce cap ...
Providing services with a high quality that are satisfying the requirements
Appling the specifications and legalizations to ensure the quality of service.
Best utilization of resources for continually improving the business activities.
CDGA keen to selects highly technical instructors based on professional field experience
Since CDGA was established, it considered a training partner for world class oil & gas institution
3012, Block 3, 30 Euro Business Park, Little Island, Co. Cork, T45 V220, Ireland
Mon to Fri 09:00 AM to 06:00 PM
Contact Us anytime!
Request Info