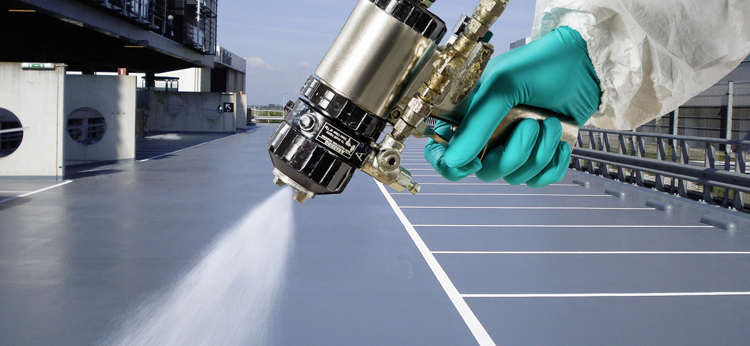
This coatings short course trains the participants with the knowledge and skills required for effective coatings inspection, maintenance and repair of both organic coatings (or paints) and metallic coatings such as hot-dip galvanizing and metallic spray or metallization.
By the end of this course delegates will learn about:
Engineers and technologists who are in charge of cathodic protection systems, Designers who are interested in cathodic protection technology for corrosion prevention, Technicians and maintenance personnel who deal with installed cathodic protection systems, Facility owners and users who are concerned with corrosion, Plant Maintenance Engineers and Supervisors, Materials Engineers, Design, Manufacturing, Mechanical and Inspection Engineers, Quality Assurance/Control Personnel, Chemical Treatment Personnel, Protective Coating and Lining Personnel
The Role of a Coating Inspector
Corrosion Concepts Relevant to Coatings
BS & ISO Classification of Corrosive Environments
Characteristics of Coatings
Fundamentals of Coatings
The Protective Coating System
Corrosion Resistant Organic Coatings
Corrosion Resistant Zinc Coatings: zinc-rich coatings vs. hot-dip galvanizing
Designing for Coatings
Effect of Substrate on Coating Life
Importance of Surface Preparation
BS, ISO, SIS, NACE, SSPC Standards Relevant to Surface Preparation
Methods of Application
Health and Safety Aspects
Selection of Coatings
Coatings and Cathodic Protection
Coating Failures: Causes and Prevention
Coating Repair and Maintenance
Development of Coatings Specifications
Quality Control in Coatings Application
Coatings Inspection and Testing
CDGA attendance certificate will be issued to all attendees completing a minimum of 80% of the total course duration.
Code | Date | Venue | Fees | Register |
---|---|---|---|---|
FAC136-04 | 23-11-2025 | Dubai | USD 5450 |
This course provides advanced level technology topics related to protective coatings. Highlights include an in-depth discussion of coatings, their basic chemical properties and any unique consideratio ...
This course thoroughly and systematically covers every aspect of coatings application and inspection techniques, maintenance and repair procedures. Coatings selection, specifications, applications and ...
This course thoroughly and systematically covers every aspect of coatings application and inspection techniques, maintenance and repair procedures. Coatings selection, specifications, applications and ...
PCS 1 Basic Principles provides an introduction of coatings and linings used to control corrosion as well as the economic benefits of managing them. This course defines and examines common coatings us ...
Providing services with a high quality that are satisfying the requirements
Appling the specifications and legalizations to ensure the quality of service.
Best utilization of resources for continually improving the business activities.
CDGA keen to selects highly technical instructors based on professional field experience
Since CDGA was established, it considered a training partner for world class oil & gas institution
3012, Block 3, 30 Euro Business Park, Little Island, Co. Cork, T45 V220, Ireland
Mon to Fri 09:00 AM to 06:00 PM
Contact Us anytime!
Request Info