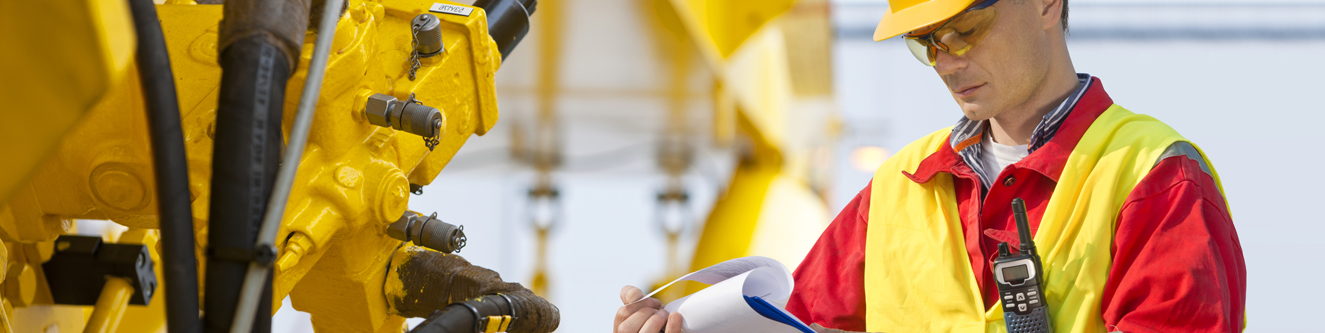
Reliability Excellence for Managers is ideal for corporate and plant managers, as well as those engaged in continuous improvement initiatives such as Lean, TPM and Six Sigma. Suggestions include Chief Operating Officer, V.P. Operations, General Managers, Plant Managers, Corporate Reliability Managers, Maintenance Managers and Operations Managers.
Session 1 - Building the Foundation for Rx
Session 2 – Leading and Managing Change
Session 3: Best Practice Business Processes and Optimization
Session 4 – Sustaining Reliability and Continuous Improvement
CDGA attendance certificate will be issued to all attendees completing minimum of 80% of the total course duration.
Code | Date | Venue | Fees | Register |
---|---|---|---|---|
MI223-03 | 14-09-2025 | Dubai | USD 5450 | |
MI223-04 | 16-11-2025 | Cairo | USD 5450 |
High plant reliability is critical for every successful company, and it has never been more important than it is in the present economic climate. The costs associated with equipment downtime and redu ...
Business process analysis and modelling is an essential component of Business Process Redesign (BPR) as well as other business process improvement initiatives such as reengineering, systems developmen ...
This course is packed with the insights and the powerful techniques of successful maintenance planning and scheduling for high equipment reliability. The comprehensive content gives you best practice ...
Providing services with a high quality that are satisfying the requirements
Appling the specifications and legalizations to ensure the quality of service.
Best utilization of resources for continually improving the business activities.
CDGA keen to selects highly technical instructors based on professional field experience
Since CDGA was established, it considered a training partner for world class oil & gas institution
3012, Block 3, 30 Euro Business Park, Little Island, Co. Cork, T45 V220, Ireland
Mon to Fri 09:00 AM to 06:00 PM
Contact Us anytime!
Request Info