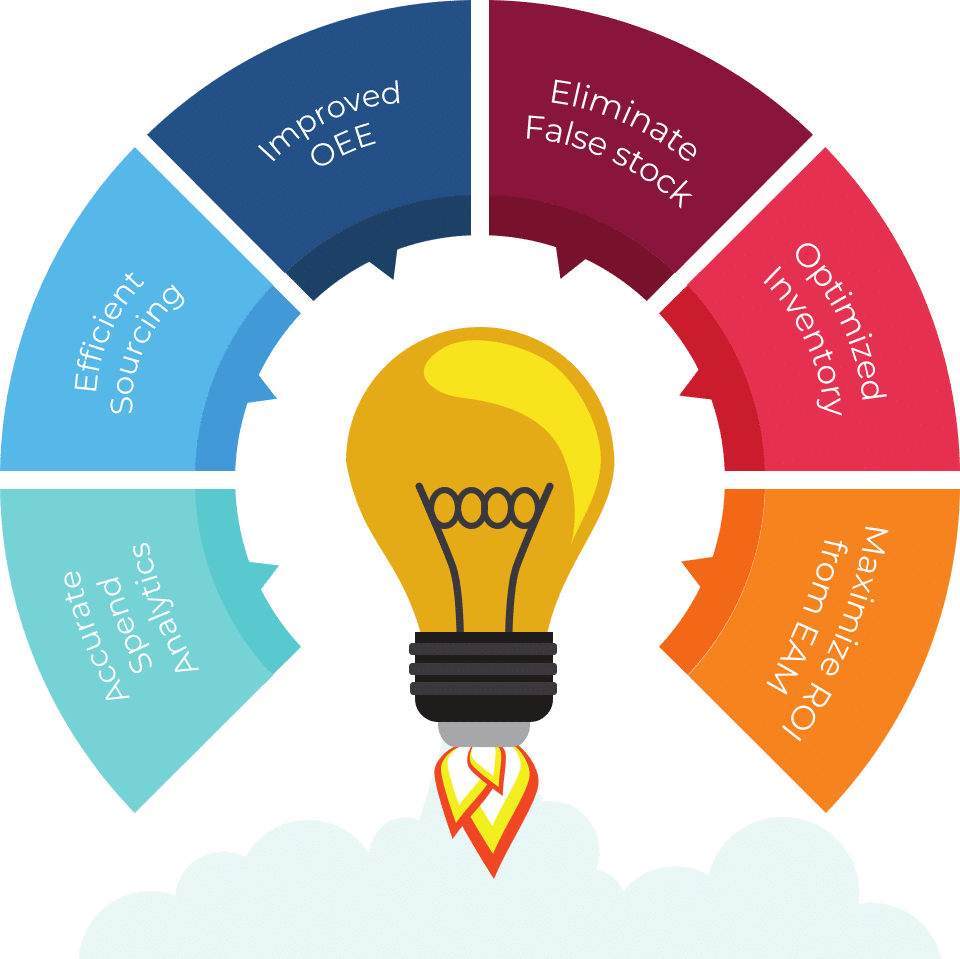
Delegates would be able to equip themselves on how to categorize and integrate master product catalogue into User’s Parts list of equipment/plant and machineries including production, maintenance and construction materials list. This Program will also provide delegates on how to effectively maintain records related to products, standards, specifications and certifications to ensure prompt provision of information including statistics and exercises related to master catalogue.
This program will be delivered by number of short and long class exercises, team working and presentation, video, situation based case studies, work-based problem solving, awareness of various Materials Management Systems and Configuration Management Systems.
Day1 - Essentials of Material Cataloguing, Specifications & Storage Planning
Day2 - Technical Integrity of the Materials Cataloguing & Storage Planning
Day3 - Commercial Integrity of the Materials Cataloguing & Storage Planning
Day4 - Enhancing Materials Catalogue Management and Optimum Storage Planning
Day5 - Materials & Storage Standards and Specifications
CDGA attendance certificate will be issued to all attendees completing minimum of 75% of the total course duration.
Code | Date | Venue | Fees | Register |
---|---|---|---|---|
PRO131-02 | 01-09-2025 | Istanbul | USD 5950 | |
PRO131-03 | 02-11-2025 | Amman | USD 5450 | |
PRO131-04 | 21-12-2025 | Dubai | USD 5450 |
Eliminating functional silos is an imperative if organizations are to achieve the high levels of customer satisfaction and reduced cost demanded of the supply chain. Eliminating these silos requires c ...
This course is aimed at both suppliers and buyers who need an overview of the key drivers involved when viewing supply chains from a logistics/demand point of view.
Supply chain management helps organizations build and deliver products better, faster and cheaper. Supply chain managers are involved in every facet of the business process – planning, purchasing, inv ...
Providing services with a high quality that are satisfying the requirements
Appling the specifications and legalizations to ensure the quality of service.
Best utilization of resources for continually improving the business activities.
CDGA keen to selects highly technical instructors based on professional field experience
Since CDGA was established, it considered a training partner for world class oil & gas institution
3012, Block 3, 30 Euro Business Park, Little Island, Co. Cork, T45 V220, Ireland
Mon to Fri 09:00 AM to 06:00 PM
Contact Us anytime!
Request Info