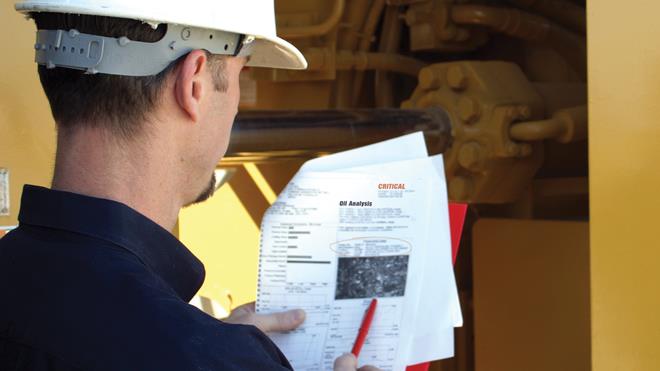
By the end of this course delegates will be able to:
Maintenance personnel & supervisors, Planning engineers, Foreman and technicians, Mechanical, electrical and operational personnel, Personnel designated as planners, or identified to become planners, Predictive and preventive maintenance, technicians & supervisors, Key leaders from each maintenance craft, Key operations personnel
The Work Planning Process
Necessary Planning Office Systems and Methods
Specifying Workmanship Standards
Inventory Purchasing and Management
Project Management Principles and Practices
Miscellaneous
CDGA attendance certificate will be issued to all attendees completing minimum of 80% of the total course duration.
Code | Date | Venue | Fees | Register |
---|---|---|---|---|
MI167-03 | 05-10-2025 | Dubai | USD 5450 | |
MI167-04 | 07-12-2025 | Cairo | USD 5450 |
Providing services with a high quality that are satisfying the requirements
Appling the specifications and legalizations to ensure the quality of service.
Best utilization of resources for continually improving the business activities.
CDGA keen to selects highly technical instructors based on professional field experience
Since CDGA was established, it considered a training partner for world class oil & gas institution
3012, Block 3, 30 Euro Business Park, Little Island, Co. Cork, T45 V220, Ireland
Mon to Fri 09:00 AM to 06:00 PM
Contact Us anytime!
Request Info