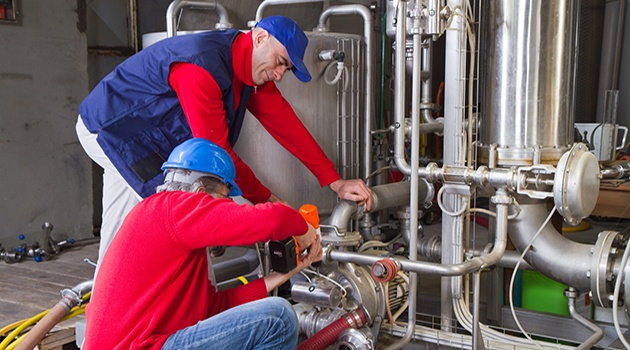
This course is structured to provide the delegates with the appropriate mix of technical fundamentals and practical best practices to maximize their learning. The material presented demonstrates some concepts that are not always shown or described in textbooks. The course emphasis is on developing a practical understanding of the inspection and maintenance requirements for fixed equipment and piping systems in process plant applications. Sample problems and participant exercises are included throughout the course to illustrate the concepts discussed and provide the delegates with practice in applying them.
By the end of this course delegates will be able to:
Engineers, Supervisors, Plant Operators, Managers, and other technical personnel who are responsible for the inspection, fitness-for-service assessments and maintenance of pressure vessels, heat exchangers, aboveground atmospheric storage tanks, and piping systems
Integrity and Reliability of Process Plant Equipment
Pressure Vessel Integrity Program
Fitness-for-Service Assessments
Pressure Vessel Inspection
Pressure Vessel Inspection Practices
Evaluating Corroded Pressure Vessels for Continued Operation
Brittle Fracture Assessment
Details for Welded Repairs and Alterations
Rerating Pressure Vessels
Changes to Original Design Conditions
Hydrostatic Test Requirements
Glossary
Heat Exchanger Maintenance
Evaluating the Suitability of Corroded Components
Typical Maintenance and Inspection Procedures
Rerating Exchangers
Piping Inspection and Evaluation
Piping Materials and Modes of Failure
Piping System Repair, Alteration, Rerating, and Pressure Testing
Flange Joint Assembly and Bolt up Procedure
Guidelines for Hot Tapping (Pressure Tapping)
Appendices
Glossary
Aboveground Storage Tank Maintenance
Introduction
Tank Inspection
Tank Component Evaluation
Tank Repair and Alteration
Dismantling and Reconstruction
Examination and Testing
CDGA attendance certificate will be issued to all attendees completing minimum of 80% of the total course duration.
Code | Date | Venue | Fees | Register |
---|---|---|---|---|
MI163-03 | 26-10-2025 | Riyadh | USD 5450 | |
MI163-04 | 21-12-2025 | Dubai | USD 5450 |
Designing process plants is a complex and demanding process. The design of plant layout is one of the most important tasks before plant construction. A successful plant layout will not only reduce cap ...
• Pressure vessels, heat exchangers, above ground atmospheric storage tanks, and piping systems typically represent over half the capital investment in a process plant. Mechanical engineers at end-use ...
Start Up and Commissioning of new plant and equipment presents both a major technical and management challenge. An organisation’s personnel must familiarize themselves with new equipment, processes an ...
There is an alarming trend in industry to discount the potential contribution of the Technical/Operations function to productivity improvement, product quality and gains in market share. Principles ta ...
Providing services with a high quality that are satisfying the requirements
Appling the specifications and legalizations to ensure the quality of service.
Best utilization of resources for continually improving the business activities.
CDGA keen to selects highly technical instructors based on professional field experience
Since CDGA was established, it considered a training partner for world class oil & gas institution
3012, Block 3, 30 Euro Business Park, Little Island, Co. Cork, T45 V220, Ireland
Mon to Fri 09:00 AM to 06:00 PM
Contact Us anytime!
Request Info